Bridging Information Gaps for Advanced Production Strategies in Industry
In the cutthroat world of manufacturing, data-driven decision-making has become a necessity for success. With customers demanding quality, timely delivery, and price-consciousness, the margin for error is slim. Instead of relying on old-school methods, modern manufacturers are leveraging insights from their operational systems across the front office and shop floor to make well-informed choices.
However, a recent survey by Dassault Systèmes revealed that 20% of manufacturers are still making poor decisions due to lacking or unreliable data. By contrast, 70% or more of respondents reported significant improvements in areas like quality control, production efficiencies, and sales when reliable manufacturing data was available.
The secret to control and visibility of the manufacturing cycle lies in filling the data gaps that often exist between front-office planning operations and actual production execution, quality assurance, and shipping operations. To succeed, it's not just about planning well - it's also about knowing when production delays or quality issues have disrupted your plans and taking immediate action to rectify them.
Take SAY Plastics, for example. By using dashboards, advanced production tracking, and alert systems in its ERP system, SAY Plastics can monitor production timelines, identify bottlenecks, adjust schedules on the fly, and optimize resource allocation to meet deadlines. Real-time insights via dashboards and alerts enable them to swiftly address any supply chain issues. As a result, SAY Plastics has seen a dramatic improvement in its on-time delivery rates, which are now near 100%.
Production performance and quality control were two areas in the survey where the largest gaps were found. These areas often have isolated management systems that are disconnected from the primary manufacturing operating system. Bridging these data gaps necessitates integrating the results from production monitoring, process monitoring, and quality inspections into the information flow that informs the front-office planning and customer relations teams.
This is where SIGN Fracture Care offers a great example. SIGN, a medical device manufacturer registered with the FDA and ISO 13485-certified, has closed the gap between quality control and the rest of the organization by automating its processes using the ERP system's quality modules. This enables them to trigger and document all inspections, schedule and document gauge calibrations, and store all data digitally for easy access and compliance with regulations.
In-line quality inspections validate the acceptability of work in process as it progresses to finished goods. Production and process monitoring play a central role in supporting these inspections, track a work order's progress through production, and verify whether tooling and equipment are performing to specifications. Without real-time production, process, and quality information, planners often schedule jobs and materials into work centers that are occupied with previous production tasks, leading to compounding problems.
By creating a closed information loop that bridges shop-floor results and front-office software, manufacturers can ensure that their planning is realistic and adjust resources accordingly. This is why many manufacturers are investing heavily in connecting their ERP, manufacturing execution, and quality assurance systems either through system integration or adopting platforms with native integration.
Here are five areas where manufacturers are using integrated planning, production, and quality data to improve their performance:
- Quality Control (47%): Data-driven quality control can be achieved through in-process inspections which are forced by the quality control module. Operators record periodic measurements, and if a measurement fails to occur, supervisory personnel are notified.
- Business Strategy (43%): By gaining access to actual cost data, driven in part by shop floor process and production monitoring, manufacturers can produce product and customer scorecards to identify their most profitable products, require price updates, and identify top contributors to overall profitability.
- Customer Service/Support (36%): ERP system's capable-to-promise feature can give customer service representatives the information they need to provide fact-driven delivery time frames to customers.
- Operator Performance (34%): Automatically tracking cycle times for both operators and machines using production and process monitoring provides management teams with accurate runs-best information for better resource allocation.
- Order Management (32%): By identifying a best path forward based on real-time data from production and process monitoring, quality inspections, inventory management, and supply chain management, manufacturers can optimize production schedules and prevent late deliveries or costly rush delivery fees.
In conclusion, manufacturers are closing the data gaps between planning and execution by implementing various strategies, like integrating software systems, employing data-driven decision making, and automation and digitization. By doing so, they improve efficiency, accuracy, and cost reduction, leading to a more cohesive and efficient production environment and ultimately better performance and profitability.
- In the manufacturing industry, data-driven decision-making is crucial for success, as it helps in making well-informed choices across all operations, from front-office planning to shop-floor execution.
- However, a survey by Dassault Systèmes shows that around 20% of manufacturers are still making poor decisions due to the lack or unreliability of data.
- By contrast, manufacturers who have access to reliable data see significant improvements across various areas, such as quality control, production efficiencies, and sales.
- One solution to fill data gaps is by integrating the results from production monitoring, process monitoring, and quality inspections into the information flow that informs the front-office planning and customer relations teams.
- For instance, SAY Plastics improved its on-time delivery rates nearly to 100% by using dashboards, advanced production tracking, and alert systems in its ERP system, allowing them to monitor production timelines, identify bottlenecks, adjust schedules, and optimize resource allocation.
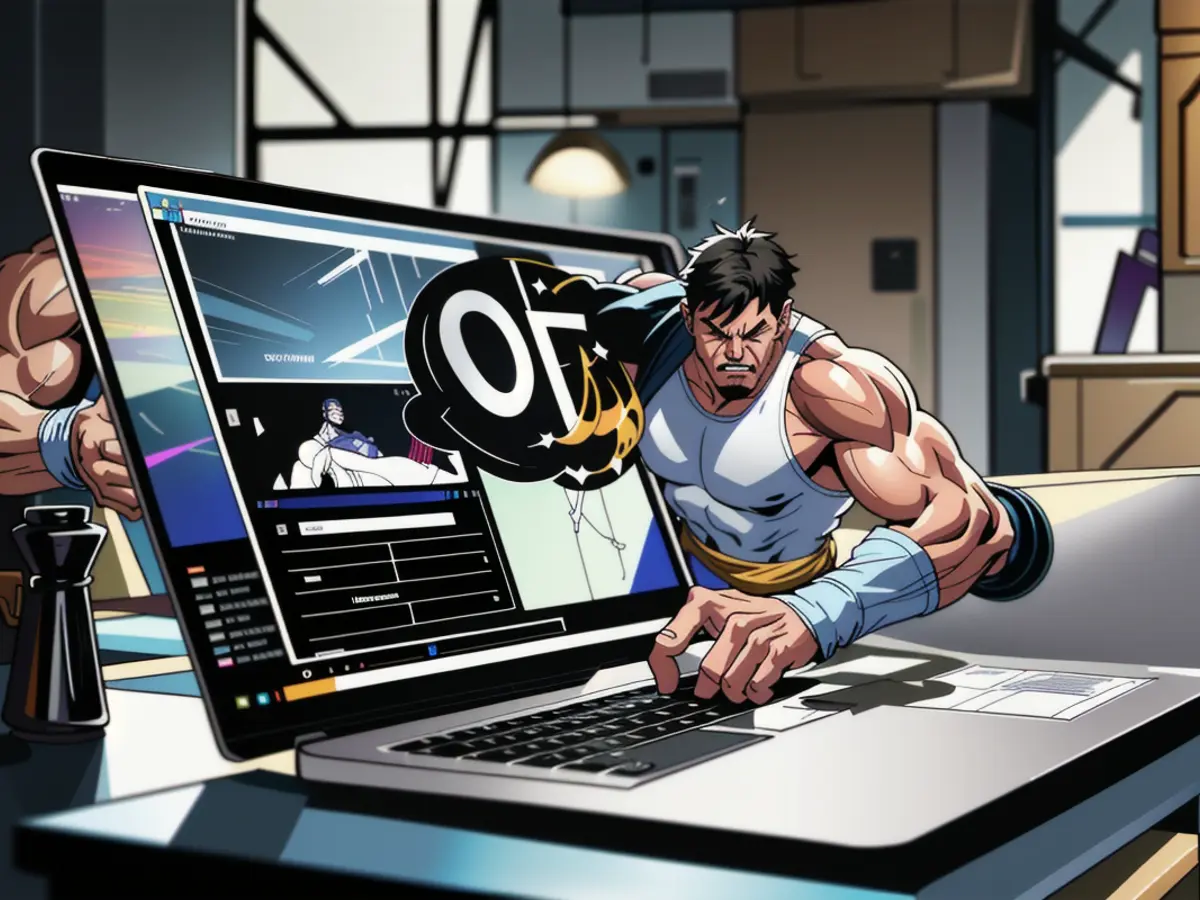
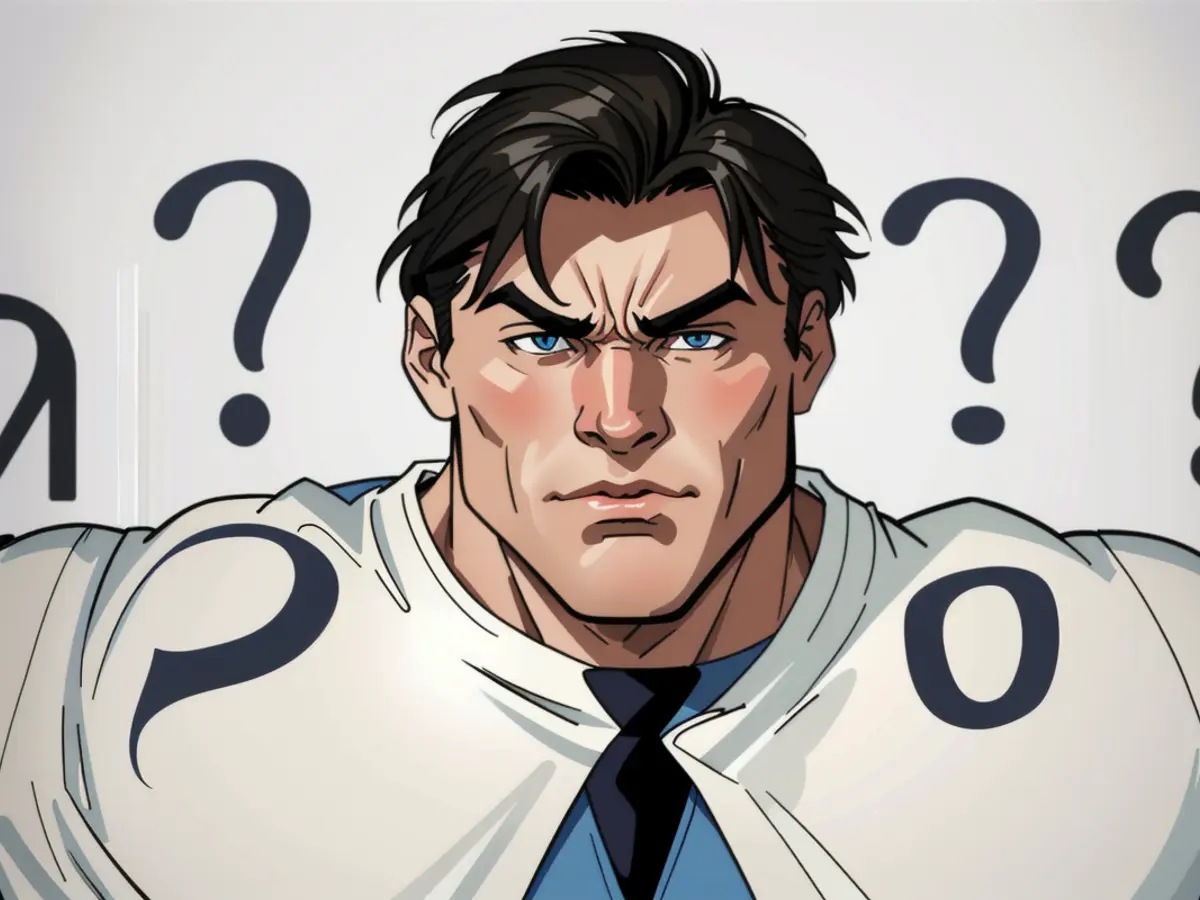
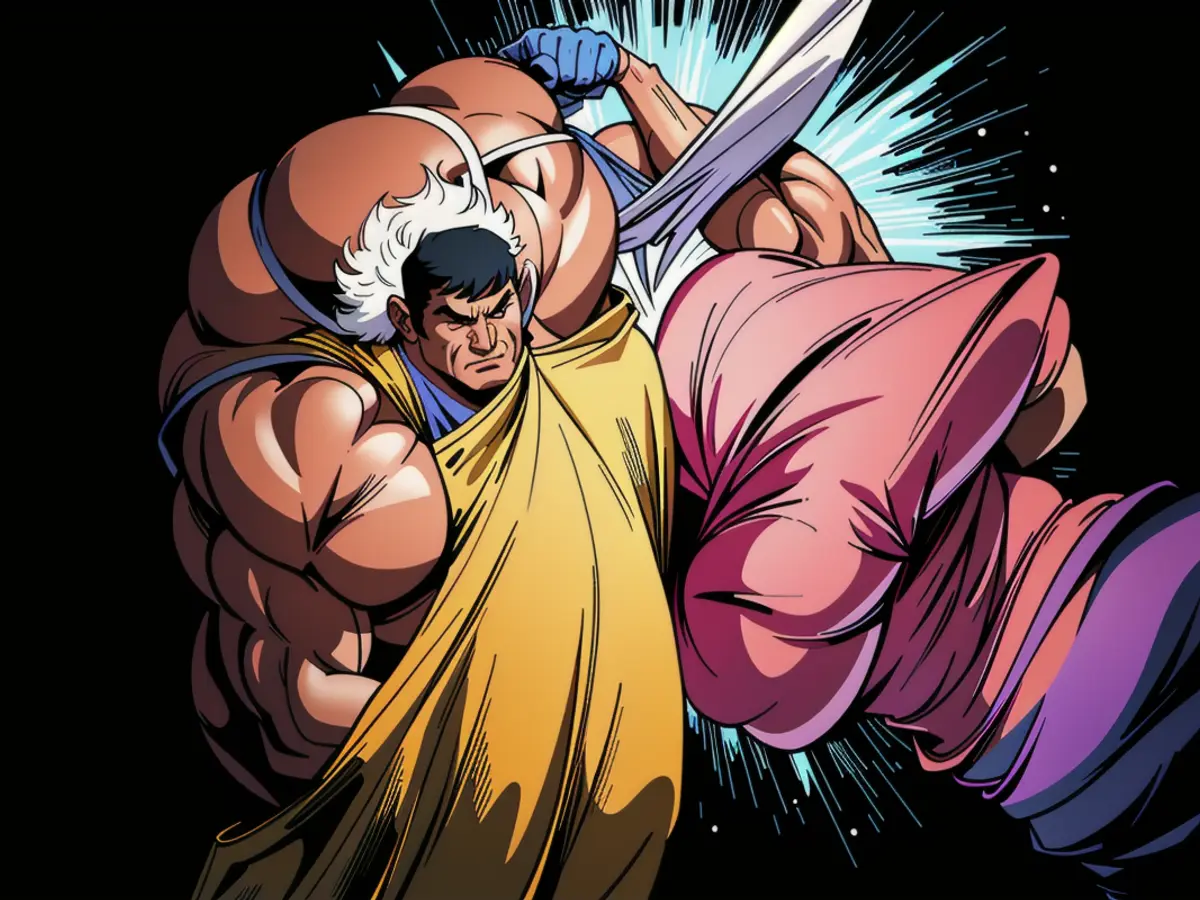